Pneumatic Tube System in one of the largest Chemical Complexes
Key facts
- Bridging of up to 4.8 km with hot, corrosive and liquid goods in an industrial laboratory
- 100% reliability of the intralogistics thanks to redundancy
- Development of an individual carrier specific for the customer’s requirements
- Integration into the laboratory information system of the customer
Our client
Our client is a chemical company, that produces more than 3 million tons of high-quality plastics and specialty chemicals every year. 26 integrated manufacturing plants are based on an area of 6 km². It is obvious that such an area has to be bridged by a transport system.

Challenging transport of specimens
The customer’s developing process is highly dependent on the internal quality management system. This demands, that chemical specimens are taken and analyzed as promptly as possible to prevent a delay of the following processes. Therefore the specimens have to be conveyed from the 4.8 km distant buildings to the central laboratory building. And this should be done best around-the-clock without downtimes due to troubles or maintenance services.
However, this is not possible with any transport system. No system can guarantee 24/7 reliability. Nevertheless, Hörtig offered a convincing solution: By using two similar systems, transport at any time is ensured. The following processes can smoothly take place without any delay.
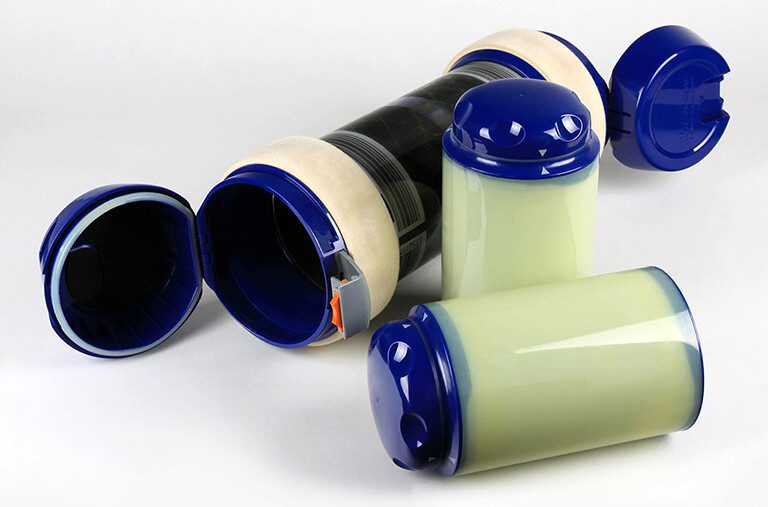
Safety of the transported good
At the company, dangerous goods are transported. The carriers have to convey fluid, hot and corrosive material safely via the whole company ground. Hörtig especially developed a transport carrier that matches these individual requirements of the client.
This carrier is pressure-resistant until 200 millibar and applicable in manifold ways for diverse specimens. Due to the thermal isolation, 150°C hot specimens have a temperature of 120°C still, when arriving at the laboratory after 20 minutes of transport. Thus specimens are conveyed safely, secure and in proper quality.
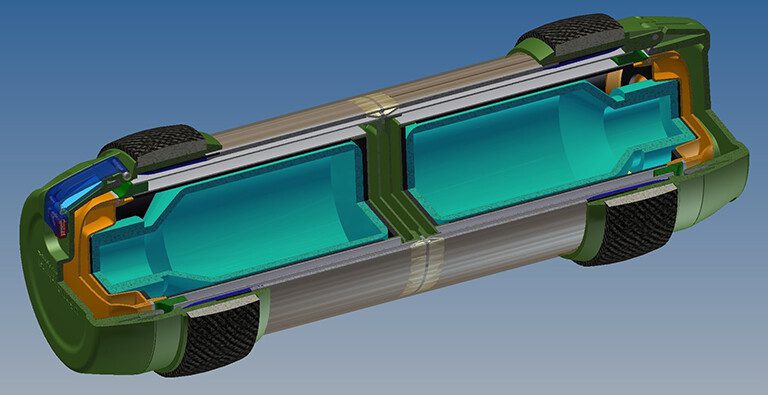
Decision on the pneumatic tube system
The responsible persons weighted up all transport options critically and finally decided on installing a smart pneumatic tube system type H61 from Hörtig Rohrpost. This impressed with three main issues: Safety, security, and cost-effectiveness. The expenses for the pneumatic tube system were only 35 % of the ones for alternative transport options.
Hörtig system
Now, the tube lines spread over the whole company area. Up to 4.8 km at a stretch are overcome by the pneumatic tube system with all sorts of specimens. To avoid utilizing the highly frequented floor area even more, the tube lines had been installed by means of pipe bridges. Through the smart integration of the pneumatic system in the laboratory information system, it is possible to generate, save and analyze important information. The customer knows for example always, which specimen is in which carrier at which place in the company.
The system is an integral part of the business processes and contributes significantly to a smoothly running operating procedure by conveying up to 500.000 specimens per year.
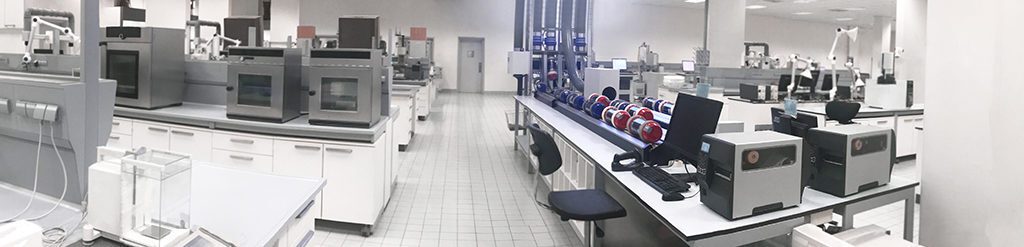
Customer’s pneumatic tube system
- 92 pneumatic tube stations with 28 km tube length and 67 zones connect 15 buildings with four lab departments
- 4 Hörtig lab benches for sending and receiving of specimens
- Conveying 500.000 specimens per year with a rate of 1.200 carriers per day
- Smart system thanks to Ethernet
- 100 % reliability with 24/7 transport due to two redundant systems
The use case as PDF: our references